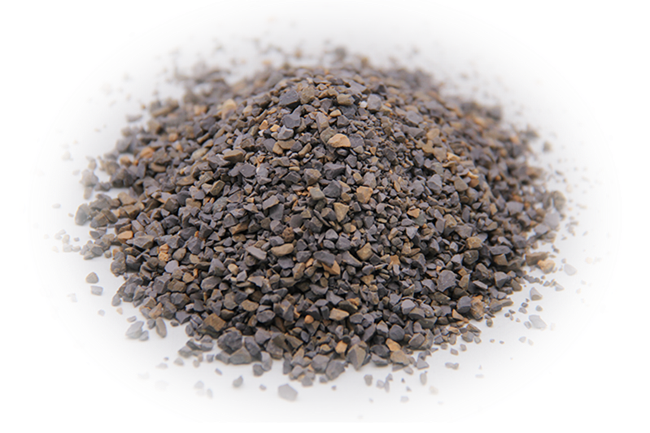
Zirconia is a material known for its high strength, toughness, and resistance to wear and corrosion. Its use in refractory materials has been steadily increasing due to its superior properties, making it a popular choice in applications where durability and long-lasting performance are critical. On the other hand, aluminum oxide is also a widely used material in the refractory industry, valued for its high thermal conductivity, hardness, and chemical resistance. Both materials have their own strengths and weaknesses, and choosing between them depends on the specific requirements of the application.
When it comes to the manufacturing and trading of refractory and abrasive raw materials, HENAN JUNSHENG REFRACTORIES LIMITED has over 20 years of experience in producing high-quality materials. The company has invested in advanced science and technology, modern equipment, and strict process management to ensure the production of top-notch materials that meet the needs of their customers. With their expertise in the field, they are well-equipped to provide valuable insights into the properties and applications of zirconia and aluminum oxide in refractory materials.
One of the key differences between zirconia and aluminum oxide lies in their mechanical properties. Zirconia is known for its high strength and toughness, making it an ideal choice for applications that require resistance to wear and high mechanical stress. This makes it suitable for use in high-temperature environments, such as in the production of ceramics, glass, and steel. On the other hand, aluminum oxide is valued for its hardness and thermal conductivity, making it a popular choice for applications that require high levels of abrasion resistance and thermal insulation.
Another important factor to consider when comparing zirconia and aluminum oxide is their chemical properties. Zirconia has excellent resistance to corrosion and can withstand harsh chemical environments, making it suitable for use in applications where exposure to corrosive materials is a concern. Aluminum oxide, on the other hand, also exhibits good chemical resistance and can withstand high temperatures, making it suitable for use in a wide range of industrial applications.
In addition to their mechanical and chemical properties, the cost and availability of zirconia and aluminum oxide are also factors to consider when choosing between the two materials. Zirconia is known for being more expensive than aluminum oxide, due to the higher cost of production and the limited availability of raw materials. This makes zirconia a more premium option for applications that require its unique properties, while aluminum oxide provides a cost-effective alternative for applications where its properties are sufficient.
With their extensive experience in the industry, HENAN JUNSHENG REFRACTORIES LIMITED understands the importance of choosing the right materials for specific applications. Their range of high-quality refractory materials, including both zirconia and aluminum oxide, provides customers with options that are tailored to their individual needs. Whether it's for high-temperature applications, corrosive environments, or abrasive materials, the company is committed to providing the best solutions for their customers.
In conclusion, both zirconia and aluminum oxide have their own unique properties and applications in the refractory and abrasive industry. While zirconia offers high strength, toughness, and resistance to wear and corrosion, aluminum oxide provides hardness, thermal conductivity, and chemical resistance. With their decades of experience and dedication to producing high-quality materials, HENAN JUNSHENG REFRACTORIES LIMITED is well-equipped to provide valuable insights into the comparison between these two materials and guide customers in choosing the right option for their specific needs.